Common Workplace Injuries and How to Prevent Them
Nobody likes to think of taking a nasty tumble or coming a cropper – whether at home, work or at play. Having a horrid run-in with a trolley in the supermarket, tripping over the dog, or suffering a sprain on the squash court could happen to the best of us. But did you know that injuries in the workplace can be just as likely, and may be are more common than you think?
All manner of mishaps and injuries can occur in the workplace, which can cost both the employer and the employee valuable time and money. Not to mention the potential for significant implications from a health and safety point of view.
In this blog, we're going to examine the most common workplace injuries and offer some safety tips to help you prevent them from occurring.
Keeping tabs on tumbles and troubles
Workplace injuries cannot simply be swept under the carpet. Whether it's relatively minor (okay, paper cuts may not qualify) or major – there are policies and protocols in place to deal effectively, safely and legally with any type of injury in the workplace.
Many resources document how health and safety measures can be made simple for employers and employees. The Health and Safety Executive website is for employers and those who want basic information on what they must do to ensure their businesses comply with health and safety laws.
RIDDOR takes the riddle out of workplace wobbles
If somebody at your work premises gets injured, you must be aware of RIDDOR or the Reporting of Injuries, Diseases & Dangerous Occurrences.
According to the official site, "RIDDOR puts duties on employers, the self-employed and people in control of work premises (the Responsible Person) to report certain serious workplace accidents, occupational diseases and specified dangerous occurrences (near misses)".
Getting a handle on health and safety
According to The Health and Safety Act at Work 1974, employers are required to ensure the "health and safety of all employees and anyone affected by their work, so far as is reasonably practicable, which means balancing the level of risk against the measures needed to control the risk in terms of money, time or trouble. This includes taking steps to control slip and trip risks".
Employees have a duty to take care of their own health and safety and that of others and must use any safety equipment provided. However, it's just as critical that employers and business owners must have the correct safety signage and equipment available to keep everyone safe and sound.
Signage for all dangers in the workplace
Businesses and organisations are responsible for ensuring that staff and visitors remain safe whilst on their premises. In workplaces worldwide, signs warn of potential commonplace workplace risks and dangers that help ensure compliance with safety procedures.
These warning safety signs cover all scenarios where a potential danger may occur in the workplace, including signs for:
- Caution - "Slippery Surface", "Noise hazard - Ear Protectors must be worn", "Very Hot Water", "Trip Hazard" etc.
- Warning - "Construction Site", "Mind Your Head", "Fork Lift Trucks" etc.
- Danger - "Highly Flammable", "Electric Shock Risk", "Danger of Death", "Hazard Area – Do Not Enter Here"
Some danger signs, caution signs and hazard signs are combined with blue and white mandatory signs and red and white prohibition signs. There are also CCTV Signs (a legal requirement to comply with the data protection act when a CCTV system is in use) to notify the public of their use.
The most common reasons for injuries in the workplace are:
Being struck or caught by moving machinery
Cause: Accidents may happen to anyone working with heavy machinery; however, they are more common in construction, factories, and farms. Machinery that's not correctly guarded is a safety hazard. The results are often disastrous or even deadly when body parts get caught or struck by exposed moving parts or flying objects from machines without protective guards.
Prevention: The best way to circumvent mechanical hazards is to remember that any machine part, process, or function that can cause injury must be safeguarded. Appropriate operator training, as well as protective clothing, should always be provided.
Trips, slips and falls
These injuries account for one-third of all personal injuries in the workplace, and they're the number one cause of all workers' compensation claims.
Cause: Slip hazards include poorly marked wet floors, icy steps or walkways and oil spills. Employees are also more susceptible to tripping in cluttered workspaces or where lighting is insufficient. Fall hazards are more common in construction, as workers spend much of their time on scaffolding, roofs and ladders. Trip hazards include clutter, poor lighting, wrinkled mats or carpets, irregular walking surfaces and uncovered cables.
Prevention: Proper signage, preventative measures (e.g. salting or gritting ahead of snow or sleet), quality walking surfaces, clean workplaces, cover loose cables with cable covers, use personal protective equipment and proper footwear. Employees should be encouraged to report areas where obstruction, spillage, clutter or damage has occurred.
Fire & Explosions
Causes: Explosions and fires have the highest casualty rate of all probable workplace accidents. Explosions and fires in the workplace are often caused by open flames, faulty gas lines or improperly stored combustible materials. The resultant injuries include burns, damage to the respiratory system, and even disfigurement or death.
Prevention: Material safety data sheets for all chemicals should be kept on hand, COSSH cabinets should be available for storage of hazardous chemicals, and employees should be required to wear personal protective equipment at all times.
Overexertion and Repetitive Stress Injuries
Causes: Musculoskeletal disorders are the costliest workplace injuries. These injuries contribute to productivity loss and millions in annual health benefit pay-out costs. Repetitive Stress Injuries (RSIs), sometimes referred to as Repetitive Strain Injuries, are the fastest growing category of workplace injury and comprise more than 100 different types of job-induced injuries. They could eventually permanently impair a worker's ability to perform their job. RSIs can be caused by improper lifting or manually lifting heavy objects.
Prevention: Lift with your knees, not your back. Short breaks and stretching are needed with repetitive work, or the work may eventually result in wear and tear on the body. Constant typing and clicking places strain on tendons and muscles. Ergonomics is the science of adjusting the job to fit the body's needs and provides injury prevention solutions that are simple and relatively inexpensive.
Vehicle Related Accidents
Causes: Accidents include falling from a vehicle, being struck by objects falling from a vehicle, being struck or run over by a moving vehicle and getting crushed by or stuck under an overturned vehicle.
Prevention: Focus on workplace design, ensuring all routes segregate vehicles and pedestrians and make any obstructions visible. Speed limit, directions and priority signs are also advisable.
In summary: the best way to protect your employees and help prevent injuries in your workplace is to take a holistic and proactive approach to workplace safety. This means ensuring that your employees have the proper protective equipment and adequate training to perform their jobs and that your facility complies with government and industry-approved health and safety and environmental regulations.
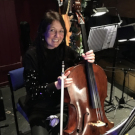
Author Bio - Debs
Digital marketer, social media, content writer, musician, sloth-lover, tea-drinker.