Protecting your Workshop Staff
Under current UK Health and Safety legislation, all employers are required to make their workplaces safe for their employees. It is their duty to make sure that no one who works for or comes into contact with their business is exposed to risks that may harm their well being. This usually means that they have to perform an assessment on the workplace to identify and dangerous and problematic areas and then come up with procedures and warnings to deal with them. However, in many workshops there are common problem areas – what are these – and what measures can businesses employ to minimise risks to their workshop staff?
Personal Safety Equipment
All staff located in the workshop should be suitably attired for the type of work in which they're engaged. Most production environments require workers to wear some kind of eye protection – usually goggles that go right the way around the eye socket and are held in place by an elastic strap. Around large industrial machinery it may also be appropriate for workers to wear ear protection in the form of hard earmuffs that fit flush against the side of the head. Other protective clothing varies with the type of work that’s being conducted, but often workers are expected to wear overalls and gloves. It’s also worth noting that there are some items workers are not allowed to wear, such as loose ties and jewellery, which present a danger as they are prone to become caught in the moving parts of workshop machinery.
Signs in the Workplace
Mandatory signs are a vital visual aid to all kinds of dangers within the workshop environment. From simple reminders that tell workers to keep their safety goggles, gloves and hard hats on near machinery to basic architectural warnings about steps and low ceilings, these signs will stop workers from injuring themselves. In large workshops signs can become even more important, alerting workers to slippery spills on the floor or broken down machinery – a situation where a broadcast might not be heard and an email most definitely won’t get read. If a workplace uses particular types of chemicals or flammable liquids that carry special hazard warning signs, then it is important that all staff receive training on what these symbols mean – and have regular tests to check their knowledge.
Machinery
All staff must be trained in the proper use of machinery in order to prevent accidents in the workshop. There should be an initial schedule of training whenever a new operator joins a company, alongside refresher courses for all existing staff to make sure that they are adhering to the correct safety procedures. In addition to this all machinery should be regularly checked in accordance with the manufacturer’s instructions to ensure it is in good working order at all times. It may also be appropriate to install master power cut-off switches for large pieces of machinery, allowing them to be stopped instantly if any kind of accident does occur. Finally, workers should report any kind of change in a machine's operation to the workshop manager as this may be an indicator that something is wrong with it.
Insulated Rubber Flooring
In workshops that use a lot of electrical equipment, including those that perform regular repairs on electric goods, tools or machinery, it is necessary to prevent against accidents involving live current that can seriously hurt or even kill a worker. Staff who are working with electricity should be made to remove all jewellery and ensure that they are completely dry before embarking on any electrical work. The best way to stop such accidents occurring is to make sure that all workers are going about their jobs in a slow methodical fashion - however it only takes an instant for something to go wrong. Workers can be protected from electrical current with rubber matting, which increases their resistance. This material should be laid right through an electrical workshop to offer as much protection as possible.
Fire-Proof Cabinets
Some workshops use all manner of solvents, glues and other chemicals, many of which are flammable. If this is the case then the workshop should use a special fire-proof cabinet where such liquids can be stored. This should have sump at the bottom to catch any spills or contain any liquid from broken or defective containers and the body of the cabinet should be specially built to withstand fires for up to an hour.
Emergency Procedures
Workshop staff should also receive training on emergency procedures in case there is an accident. There should always be a member of staff on the floor with first aid training and a fire officer, both of whom should receive regular training to make sure that they're aware of what to do following any kind of incident. In addition to this there should be regular training for all staff on general practices in emergencies, including fire drills and what to do in the event of an electrical shock.
Lead by Example
The final way in which employers can help protect their staff is by creating a workplace where safety really does always come first. By creating a pleasant workplace where all concerns are treated with importance and safety equipment and training is constantly updated and regular cycles of machine maintenance are performed, staff are not only likely to remain accident free, but will also be happier and more productive in their work. A lost employee can cost a business a large amount of money in downtime – if there is a damages claim too that this can be incredibly damaging to the company's credibility as well as economically problematic.
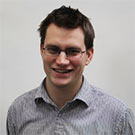